Can You Pour Concrete Without Forms?
Concrete starts off as a viscous liquid before hardening into the solid structural material that people normally know it as. The forms in a construction area help shape the area, as liquid always takes the shape of its container.
The question now is if it’s possible to install concrete without the use of forms.
No, you cannot pour concrete without forms. Concrete starts off as a viscous mixture of cement, aggregate, and water. If you don’t use forms to pour concrete, it will spread everywhere and be impossible to level properly.
In this article, we’ll be going more in-depth as to how concrete is actually used during the construction process and its different properties. Read on if you’d like to learn why construction managers do what they do or if you’re just doing research for a home DIY project.
How is concrete used?
Concrete is either poured or installed while the construction process is ongoing.
- Poured concrete is usually used for columns, foundations, and beams.
Concrete is applied this way because of these building components’ nature, which is to transmit loads of the building to the ground. As such, these parts of the building needed the strongest amount of reinforcement. When you pour concrete, it really becomes one solid mass. When pouring concrete, there should be no air pockets or anything like that left to make sure that the concrete can handle the forces as calculated.
- Pre-made concrete is used more for walls and upper floor slabs.
This is where concrete hollow blocks (CHB) comes in. Concrete hollow blocks are made in a concrete factory and are transported to the site.
What makes concrete hollow blocks so advantageous and versatile, especially for walls and floor slabs, is how light it is compared to solid concrete. Concrete hollow blocks have holes in them designed for a wide array of uses. These holes usually form a sort of “column” in the middle of the block, as such concrete hollow blocks are capable of handling the forces while still remaining light.
Concrete made in the factory
The reason why concrete hollow blocks can be produced in a factory and can be easily installed is because of set industry standards. Industry standards in the field of construction allow for quicker production of materials, as architects and engineers automatically design in accordance with these standards.
For example, most walls are actually only 0.2m (around 8 inches) wide. Knowing this, concrete manufacturers can easily mass produce this amount.
This doesn’t mean that concrete manufacturers can just make thousands of concrete hollow blocks and ship them off as soon as a client orders from them. Each and every batch must be produced within a certain timeline and will sometimes include a certain specification.
Remember, not all concrete is the same. Although concrete is made from three simple components, the different ratios and types of materials used will play a heavy role in how the concrete will perform, especially in a given environment.
For example, the concrete used at a fire exit is very different from the concrete used for structures built on top of the water. Concrete mixtures have to adjust whether it be adding special materials to the mix or using different methods of curing the concrete.
Standards for concrete
Concrete has to reliably carry a certain load once it fully cures. This is crucial for any building to remain standing for long periods of time.
The main standard that homeowners should know is that concrete is expected to handle a certain force, depending on the structure and the conditions the concrete will experience.
If the concrete is poured without a form, what would happen is that the loads will not be distributed properly, as such certain parts might experience more force than others, and this could result in a building failure.
Another important standard that is actually true for all building materials is dimensions. Uniform segments of dimensions of material ensure easy reproduction and installment. The construction market automatically assumes that standard dimensions for materials are being used, and their products are designed for that sort of area.
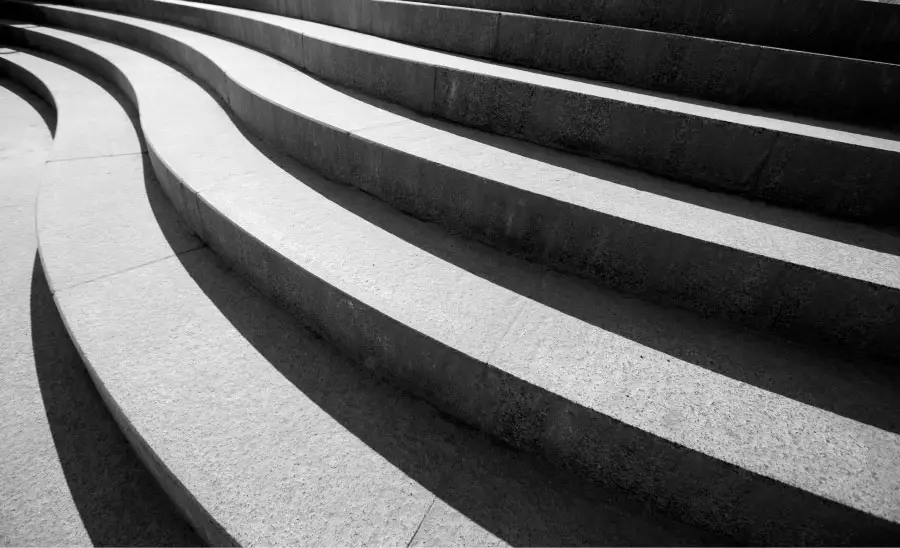
Formwork in design
Formwork is actually what opens up a different realm of opportunity for how buildings are constructed in this day and age.
Ever wondered how buildings these days manage to curve concrete as if it were curving stone?
- The formwork is first designed in such a way that captures that form.
- Rebars are added to ensure that the concrete can keep the shape and handle other loads.
- Concrete is then poured in to fill the form.
Note that how these structures are constructed takes up a lot of time and resources. They just don’t dump in concrete inside the form and call it a day. It’s a very slow process to achieve complex/unusual geometry to be able to handle loads and be constructed properly. Each section is carefully constructed to make up a better part of a whole.
Concrete and the current technology we have now, of course, makes this process a lot faster. Back in the old days, it took 40 years to build the dome for the Florence Cathedral while the dome for the Basilica of Our Lady of Peace, which has the world’s tallest dome, only took 4 years to build the entire structure.
An example of how formwork improves a house’s design is by improving the quality of how the concrete is actually set. A big signifier of quality construction is how well executed the formwork is for concrete. The sharper the edges and the flatter the wall, the better. It’s one of those subtle things that add up to a bigger picture and a better-looking house.
These days, we tend to take things for granted but just imagine that every little detail in your house was planned and designed, whether it be the small gaps in your trim to tiny details to your ceiling’s paint finish. The smaller and specific details of a building add up to a whole.
Concrete as a finish and how formwork helps
Formwork can also help provide new textures and finishes to different parts of the building, whether that be curving the walls or adding a design into the concrete to make it like shiplap.
Concrete is not only a structural material; it can also be specifically manufactured to be for finishes. For smaller areas, a special hose can be used to fill in the framework.
Another way of adding texture or finish to a wall is by imprinting formwork on a wall. You can modify your formwork to have a bit of protrusion to add depression to the concrete as it dries. However, this should only be used on concrete finishes and not structural concrete, as the uniformity of its shape is essential to the proper transfer of loads.
Conclusion
Formwork is an essential part of concrete construction. There is never a case in which it isn’t used and for a good reason. Formwork ensures that the concrete reaches its proper dimensions and properties.
Concrete is manufactured for different purposes. There are countless applications for it due to its unrivaled strength and practicality. Again, learning how to work with concrete is a requirement for any construction manager because it is essential for a project’s success.